We all know that an asphalt mixing plant is for producing hot mix asphalt by using gravel, sand, bitumen, and filler material. Continuous plants are known as asphalt drum mix plants. The basic layout of the asphalt drum mix plant is simple. The layout will have all components sorted out in an efficient manner to maximize space utilization. They are available as parallel-flow type or counter flow type. We manufacture and export both the types of asphalt drum mix plants as mobile types also.
Asphalt plant is a combination of various mechanical as well as electrical components working together to produce a specific grade of hot mix asphalt. The different types of asphalt plant components will heat aggregates, additives, bitumen, recycled aggregates to produce HMA.
In a drum mix plant, we mix gravel, sand, bitumen, and other materials in a continuous process. They are dried/heated and also mixed in a continuous process. Hence, drum mixers are also called continuous mixing of asphalt plants.
When we talk about the batch plant, it is noteworthy that they will produce HMA into batches of a specific size. The raw material will be mixed thoroughly added and mixed in a batch mixer prior to dispatch. A fixed amount of raw materials like gravel, sand, bitumen, filler material and reclaimed asphalt will be weighed prior to the addition of the same into a batch mixer.
Stationary asphalt drum mix plant layout:
A stationary asphalt drum mix plant is the most widely used asphalt mixing plant. It allows operating in less space requirement, the running cost is less and the material produced is of good quality. The number of components used is less, asphalt drum mix plant layout is as below.
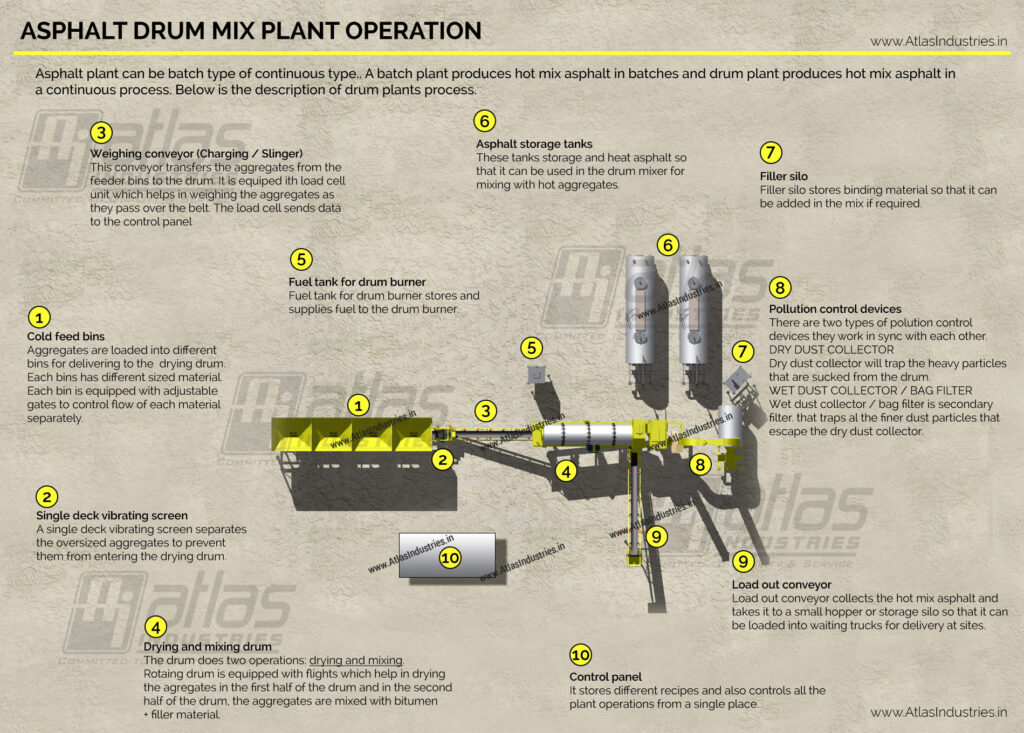
The layout of the stationary asphalt drum mix plant consists of many components laid out. The names of the components are aggregate feeding unit, single deck vibrating screen, charging conveyor, fuel tank for drum burner, drying & mixing drum, bitumen tank(s), filler addition, load out conveyor, control panel and pollution control device.
Our different installations of the stationary asphalt drum mix plant are in Nigeria, Myanmar, Philippines, Libya, Oman, Morocco, Mozambique, Libya, Botswana, Peru, Samoa, and Lebanon.
We make available different capacities of stationary asphalt drum plant like 20-30 tph, 40-60 tph, 60-90 tph, 90-120 tph, and 12-150 tph. Capacities above 150 tph are also available upon request.
Stationary asphalt drum mix plant components:
Below are the details of the stationary asphalt drum mix plant components.
- Aggregate feeding unit: Aggregate cold feeder bins are usually four to store gravel and sand in different bins as per their size. The material flow will be controlled individually from each bin.
- Single deck vibrating screen: Single deck vibrating screen will filter out all the oversized aggregates before then enter the drum.
- Charging conveyor: A charging conveyor holds the load cell. It will transfer the aggregates into the drying and mixing drum. The load cell fitted on the charging conveyor will weigh the aggregates and send data to the control panel.
- Fuel tank for drum burner: Drum burner will need a good steady supply of fuel. This tank will provide the same.
- Drying & mixing drum: Drying and mixing drum is one of the most important components of an asphalt drum mix plant. It completes two jobs. The first job is of drying aggregates, secondly, it will do the mixing of the same with bitumen and filler material.
- Filler addition unit: Mineral filler can be added separately via a mineral filler unit. It is synchronized from the control panel to have a controlled flow of the same.
- Bitumen tank: Bitumen tanks will store and supply liquid bitumen for mixing into the drum unit for mixing. The flow of bitumen will be controlled.
- Pollution control device: Usually a drum mix plant will be equipped with a wet dust collector as a pollution control device. Bag filters can also be provided with a counter-flow design asphalt plant.
- Load out conveyor with silo: Once the material is discharged from the drum load out conveyor will discharge the same into waiting trucks. Optional silo units can also be provided for the temporary storage of HMA.
- Control panel: The Control panel will house the controlling device for the asphalt plant. All the components are controlled via this control panel and it is recognized as one of the important components.
Mobile asphalt drum mix plant layout
The layout of the mobile asphalt drum mix plant is the same as its stationary counterpart. The units are designed to be mobile. This means all components of the Atlas mobile asphalt drum plant can be easily shifted from one place to another. The ease of shifting and containerized design helps in achieving the desired goal. Customers worldwide prefer this design because of the mobility factor. We have installed mobile drum mix plants in the Philippines, Nigeria, Algeria, American Samoa, Cameroon, Somalia, Botswana, Oman, Malawi, Tanzania, and Myanmar.
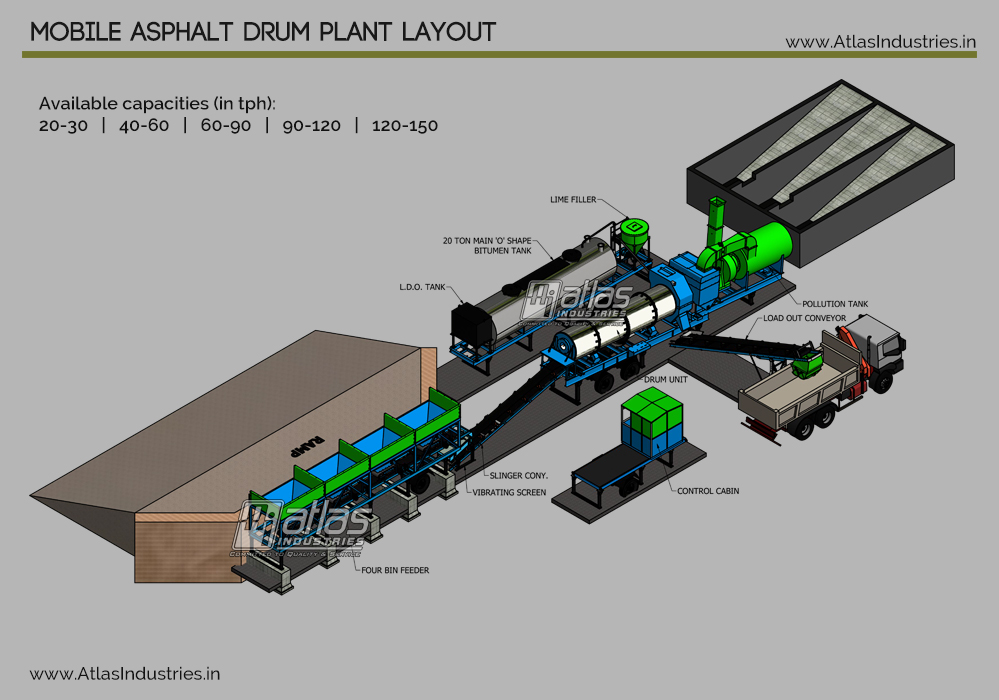
Different capacities range like: 20-30 tph, 40-60 tph, 60-90 tph, 90-120 tph, and 12-150 tph are available with Atlas. All designs are proven and sturdy. Additional bitumen tanks can also be provided upon request. Capacities above 150 tph are also available.
Mobile drum mix asphalt plant components:
Mobile asphalt drum mix plant components are the same as stationary plant components. The superior advantage that they have is in terms of mobilization. All the components of Atlas mobile asphalt drum mix plant are fully mobile. The feeder unit is mobile on one axle with pneumatic braking and king pin attachment.
• The feeder unit is mobile on one axle with pneumatic braking and kingpin attachment.
• The drying and mixing drum unit is fully mobile on two axles.
• The bitumen tank here comes on a chassis that is shared with fuel tank and mineral filler hopper. It is on one axle. Bitumen tanks can be provided with more than one axle.
• Control cabin has its own chassis with some space for Genset. This unit is on one axle.
Counter flow asphalt drum plant layout
Atlas manufactures counterflow asphalt drum mix plants in different layout options. The different capacities that we offer are 40-60 tph, 60-90 tph, 90-120 tph and 120-150 tph. The best part about this machine is that it is able to produce high-quality asphalt and also allows considerable savings of fuel. These two factors are key USP of the product enabling us to position this machine in between the traditional drum mixer and a batch plant.
We can supply counterflow asphalt drum plants in different layout and configuration options. Some of the options are as below:
- Double drum plant – Separate (counter-flow) drum for heating and a drum for mixing.
- Drum with a continuous pug mill twin shaft type mixer – Here the drum is counterflow type design and it heats the aggregates. Mixing is processed in the continuous twin shaft mixer.
- Single drum counter-flow plant – A single drum counterflow plant is equipped with a long nose burner. Heating of aggregates as well as mixing with bitumen will be accomplished in a single drum mixer.
Get mobile counterflow asphalt plant in the same capacities as a stationary plant. We have many installations of mobile type in different countries.
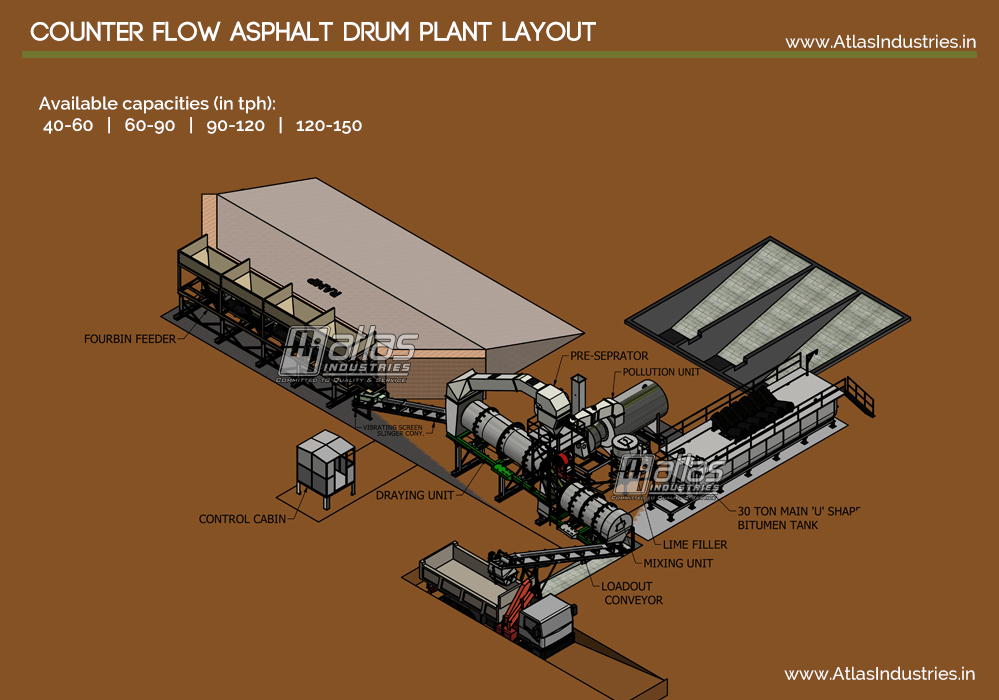
Counter flow asphalt drum plant components:
Atlas is a leading manufacturer and exporter of counter flow asphalt plants. The components of this machine are very similar to the normal drum mixer equipment. The key components are as below:
- Cold aggregate bins: Cold aggregate bins are mostly four. Any number of bins as per your requirement can be supplied. Its job is to store aggregates and sand in different bins as per their size. Each bin material flow is controlled by a variable speed drive motor.
- Single deck vibrating screen: A single deck vibrating screen is supplied here. Its job is to remove all the oversized aggregates.
- Slinger conveyor: It is used for the transfer of aggregates to the drum unit. A slinger conveyor will be fitted with the load cell. This load cell will weigh the aggregates collectively. It also sends this data to the control panel. The Control panel will control the addition of bitumen and filler material as per the input from the slinger/charging conveyor.
- Fuel tank for drum burner: A small fuel tank for a drum burner is provided. It will allow a steady supply of fuel to the drum burner.
- Drying drum: The drying drum is a counter flow type. Dust is sucked in at the entry point of aggregates. This allows aggregates to be heated evenly and heat transfer is appropriate.
- Mixing drum / Pug mill: The mixing drum in this machine is separate. Mixing is done in a drum mixer. Aggregates are blended with bitumen and filler material. In the case of pug mill – it is a continuous mixer in which all materials enter one end and exit the other end. RAP material can be added into the mixing drum or into the pug mill unit.
- Single drum counter flow mixer: Atlas also manufactures single drum counter flow asphalt mixer. This will have a long nose burner for that counterflow effect. Just behind the burner flame, bitumen will get mixed with aggregates and filler material. This type of model is more suitable if the customer wants a mobile type where they deal with only a single drum. Such an arrangement will also have an option for an addition for RAP into the second half of the drum.
- Filler addition unit: Filler unit is synchronized from the control panel to have a controlled flow. Mineral filler is added into a filler hopper. It is discharged to the mixing unit via an air compressor.
- Bitumen tank: Bitumen tanks of sufficient capacity will be provided. It is possible to increase the capacity of the bitumen tanks. It is also possible to have bigger sized bitumen tanks. Bitumen flows in a very controlled manner. It will store and supply liquid bitumen for mixing into the drum.
- Pollution control devices: A standard Atlas drum mix plant (counter flow type) will be equipped with a wet dust collector as a pollution control device. Bag filters are more efficient when it comes to pollution control. Bag filters can also be provided with a counter-flow design asphalt plant.
- Load out conveyor with silo: A heat-resistant loadout belt is provided. It will discharge material into the waiting trucks. The storage silo unit can also be provided for the temporary storage of asphalt cement material.
- Control panel: The Control panel is the main controlling device of drum mixer. All the components are controlled by a control panel. We supply the same with a microprocessor control panel or a PLC control panel.
It is very much possible to modify the layout position of Atlas asphalt drum mix plant. We usually ask customers for their preferences and layout options to fit the equipment in their available space. This helps us to maximize productivity. Get More Information Contact Atlas Industries.